At an extremely busy port, when a massive ship slowly approaches its dock, an easy berthing process is actually the reality of things. Rubber fenders dotted along dock edges play a pivotal role in keeping ships safely docked – these seemingly mundane pieces of rubber actually form part of modern ports’ safety measures.
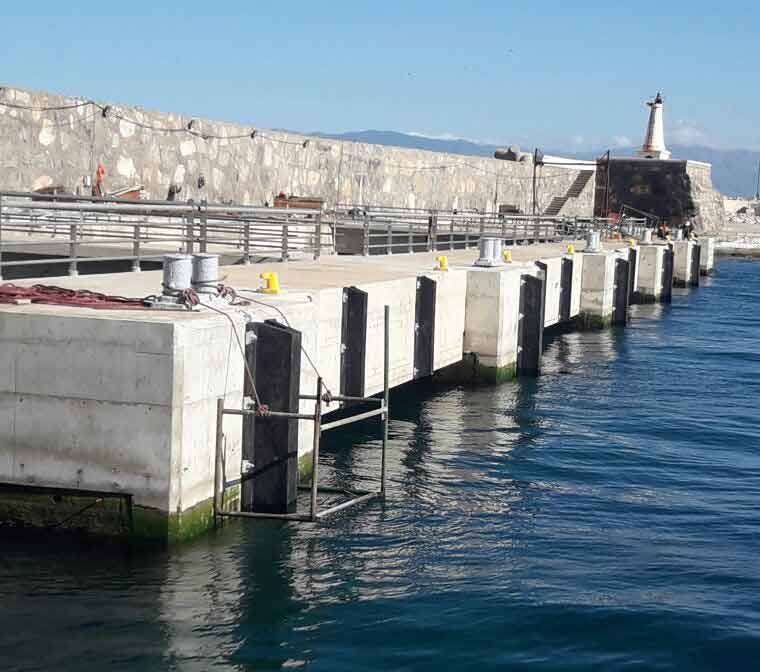
Rubber Fenders 101 – Introduction and Overview
Rubber fenders are buffers used on docks, shipyards, and vessels to absorb impact energy when ships dock at docking berths and protect structures from being damaged during docking operations. Fenders made of high-strength rubber often come equipped with built-in steel frames for increased load-bearing capacity. Furthermore, their designs range from cylindrical, D-shaped or drum-shaped structures – each tailored specifically to individual requirements.
Types and Construction of Marine Rubber Fenders
There are many types of rubber fenders with different structural designs, each suitable for specific ships and dock operations.
Common types are cylindrical rubber fenders which are easy to install. They are often best used on small to medium sized vessels.
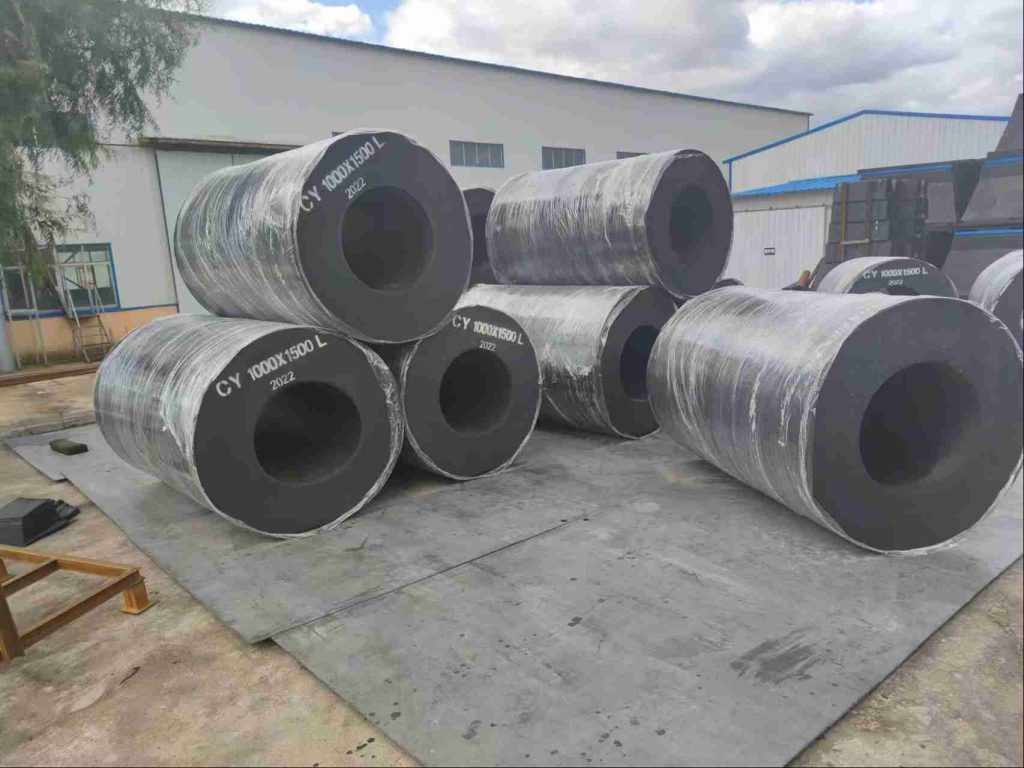
D Rubber Fenders:Â With their D-shaped cross section, D rubber fenders offer great impact resistance and are frequently found in docks.
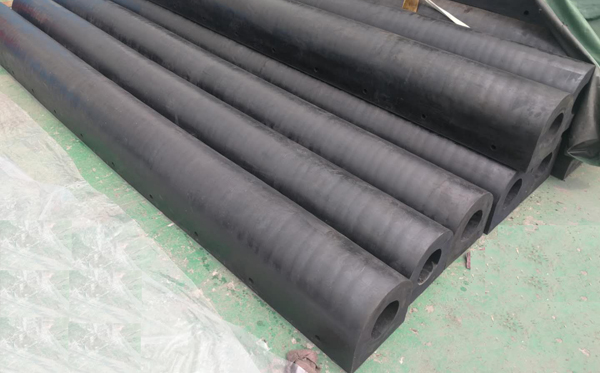
SC Rubber Fenders: Boasting an energy absorbing bulging middle design, SC fenders are perfect for large ships that need additional energy absorption.
Pneumatic Rubber Fenders:Â Pneumatic fenders offer easy transportation and storage solutions, and are commonly used for temporary berthing applications.
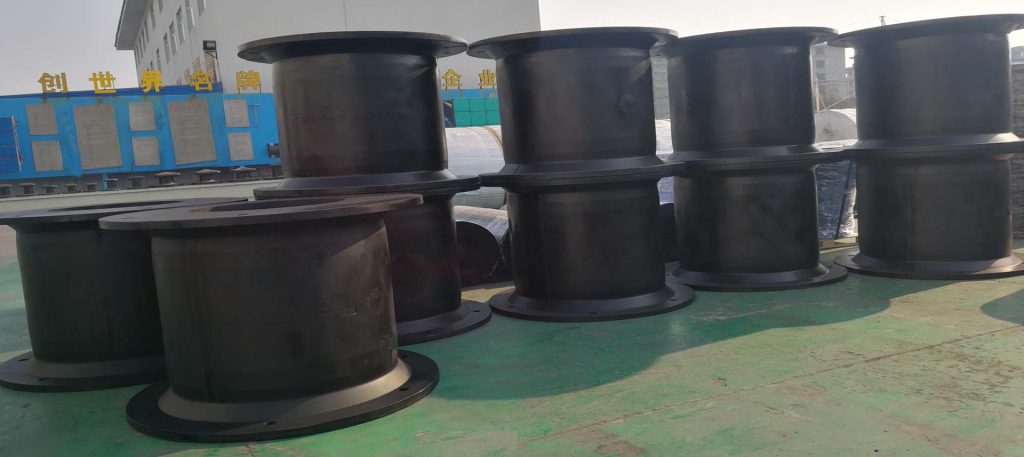
High-quality rubber fenders generally take a multi-layer design approach in terms of structure. Their outer layer usually comprises weather and seawater corrosion-resistant rubber; their middle layer could contain high strength fibers or metal skeletons; and finally their inner layer, an elastic rubber substrate. This composite structure allows high quality fenders to withstand huge impacts while still offering long service lives.
Working Principle of Rubber Fenders
Rubber fenders may appear straightforward, yet their workings contain complex engineering principles. As ships dock, massive amounts of kinetic energy must be converted into other forms through rubber fenders – this process occurs through three physical mechanisms.
Rubber materials deform when subject to pressure, storing some energy as elastic deformation. Frictional heat generation occurs as rubber molecules rub against one another, converting some of their kinetic energy into heat energy.
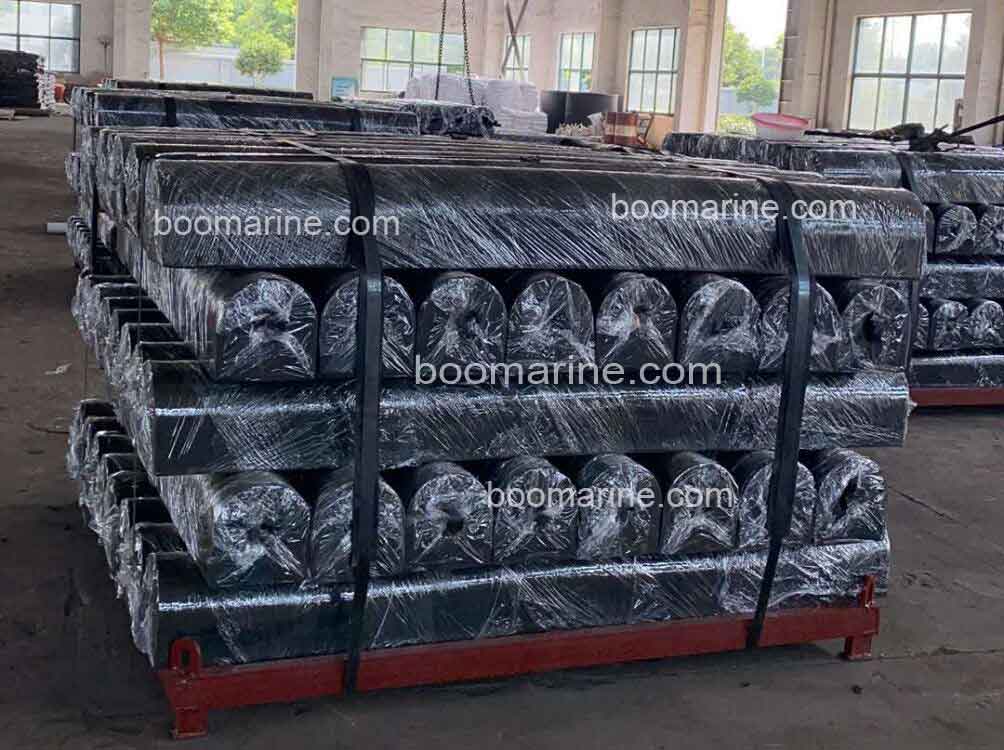
Fluid Extrusion (for certain special designs): air or liquid stored within an internal cavity is compressed, using energy and taking up space in its process.
From the time a ship enters port until its departure, rubber fenders are continually deformed and recovered – effectively absorbing impact energy from docking vessels while simultaneously reducing collision force to levels within which both they and the dock can tolerate, thus providing vital protection to both entities.
Note, however, that it’s important to remember that performance of fenders doesn’t directly equate with “softness.” An ideal fender should feature stiffness and damping characteristics suitable to effectively buffer ships without excessively rebounding and leading to secondary collisions.
Correct Selection And Maintenance Tips
Correct Selection
Selecting an appropriate rubber fender requires careful consideration of various factors.
First is the type and size of ship entering port. Since large vessels entering a port can generate significant impact forces, fenders with strong energy absorption properties, such as arched rubber fenders or drum-shaped rubber fenders, should be selected; small and medium-sized ships should opt for D-type or V-type rubber fenders instead.
Second, it is necessary to consider the use environment of the dock, including environmental factors like tide changes, water flow speed and seawater corrosion. When dealing with severe seawater corrosion issues, synthetic rubber fenders with good corrosion resistance may be best; for ports experiencing large water level variations, floating rubber fenders would likely prove more suitable.
Additionally, the speed and frequency of ship berthing will have an impactful decision regarding fender selection. Docks with fast berthing speeds and higher frequencies must use energy-absorbing fenders that provide superior energy absorption performance while offering good wear resistance to protect these vessels.
Maintenance Tips
Proper care of rubber fenders is vital to their long-term viability and ensuring safe ship docking. Here are a few maintenance tips that could extend their service life and ensure a more reliable ship docking.
Regularly inspect the surface for cracks, cuts, or abnormal wear. Clean away marine organisms and debris from its surface before checking whether fixing bolts and brackets have become loose over time. In case of significant impacts, record the condition after each major incident as well as conduct professional inspections to assess any damages sustained by professional inspectors if required.
Maintaining your fender in good condition can extend its service life up to 3-5 years and significantly lower port operating costs.
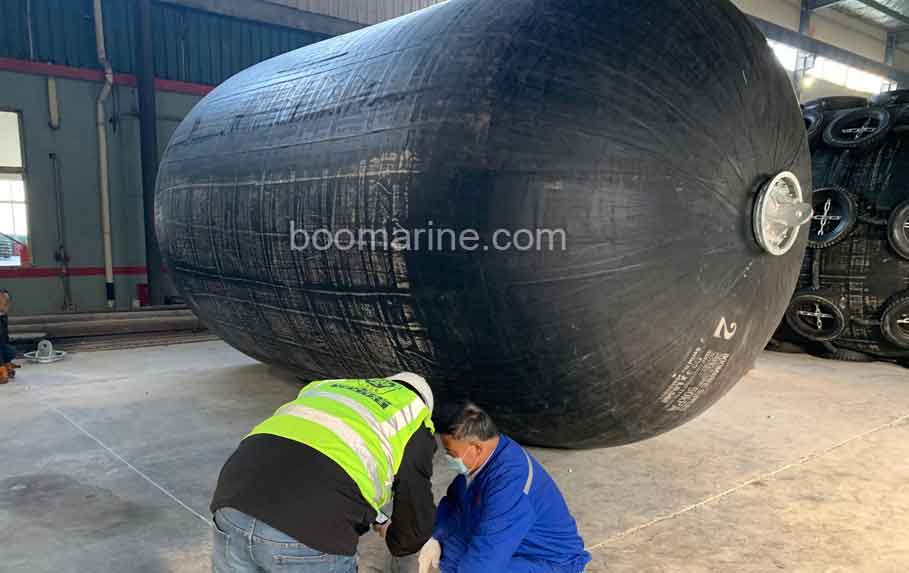
Rubber fenders may seem innocuous enough, yet they play an irreplaceable role in safe ship docking. From basic material selection and structural design through innovative working principles and scientific maintenance practices to the wisdom and care of engineering technicians – every link reflects their expertise. With the rise of the shipping industry, development comes with higher performance and quality requirements of rubber fenders, which provide more reliable protection for safe ship berthing at ports in future years.