Contents
Anchors play a critical role in maritime operations, and among the various types available, High Holding Power (HHP) anchors have emerged as a reliable choice for ensuring the safety and stability of vessels at anchor. Unlike traditional anchors, HHP anchors are specifically designed to provide superior holding capacity in a variety of seabed conditions, making them a preferred choice for both recreational boaters and commercial vessels. HHP anchors are characterized by their ability to resist dragging and slipping, offering enhanced reliability in challenging environments.
Importance of Proper Use and Maintenance HHP Anchors
While HHP anchors are engineered for robust performance, their effectiveness relies heavily on proper use and regular maintenance. Neglecting these aspects can compromise the anchor’s reliability, potentially leading to safety hazards and operational inefficiencies. Proper usage involves selecting the right type and size of anchor based on the vessel’s specifications and the prevailing seabed conditions. Additionally, deploying the anchor with the correct scope and angle is crucial for maximizing its holding power.
Maintenance is equally vital for preserving the integrity of the anchor over time. Harsh marine environments, exposure to saltwater, and the stresses of regular use can contribute to wear and corrosion. Regular inspection, cleaning, and timely replacement of worn components ensure that the anchor remains in optimal condition, reducing the risk of failures and enhancing overall safety during anchoring.
In this article, we will explore essential tips for both the proper use and maintenance of HHP anchors, providing valuable insights for maritime enthusiasts and professionals alike. By understanding the intricacies of HHP anchors and implementing best practices, users can harness the full potential of these anchors, contributing to a safer and more efficient maritime experience.
Tips for Proper Use of HHP Anchors
To fully leverage the benefits of HHP anchors, users must adhere to best practices in their selection, deployment, and monitoring. In this section, we will delve into essential tips for the proper use of HHP anchors, focusing on critical aspects such as selecting the right size and type, deploying anchors effectively, and monitoring for optimal performance.
1. Selecting the Right Size and Type of HHP Anchor for the Vessel
(1) Considerations for Vessel Size and Weight
The effectiveness of an anchor is closely tied to its size relative to the vessel it is intended to secure. Choosing an anchor with adequate size and weight ensures that it can generate the necessary holding power to keep the vessel in place, even in adverse weather conditions. Factors such as the displacement and windage of the vessel should be carefully considered to match the anchor’s specifications to the unique characteristics of the boat.
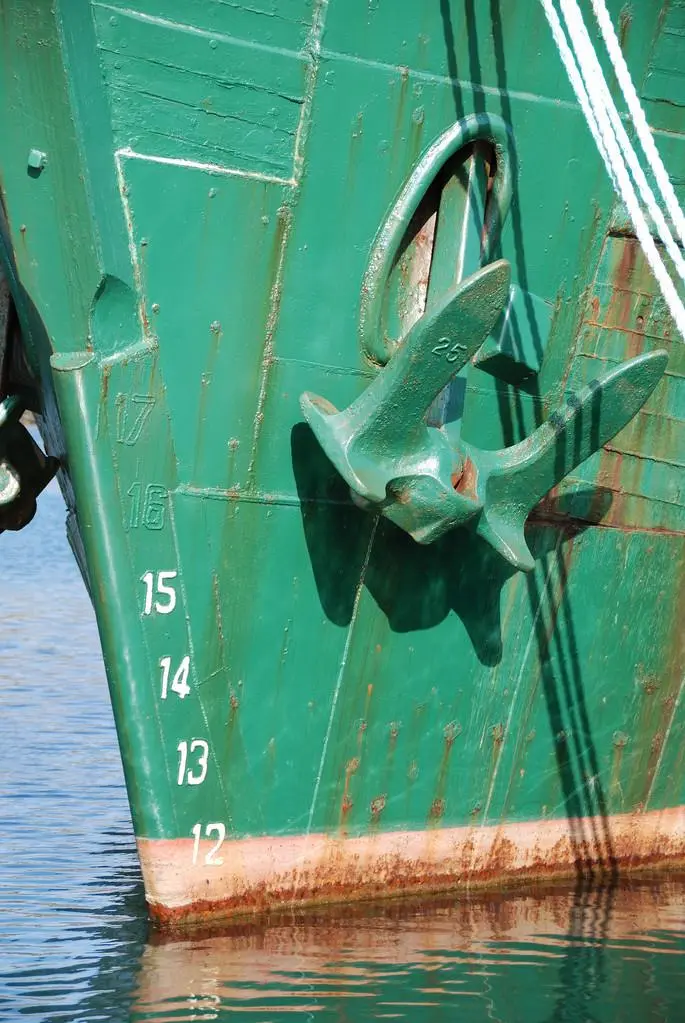
(2) Matching Anchor Type to Seabed Conditions
Seabed conditions vary widely, ranging from soft mud to hard rock, and selecting the appropriate anchor type is crucial for optimal holding power. Different anchors are designed to excel in specific seabed conditions, and understanding the nature of the seabed in the anchoring area is paramount. Whether it’s a fluke-style anchor for sandy bottoms or a plow-style anchor for mixed seabeds, choosing the right anchor type enhances overall anchoring performance.
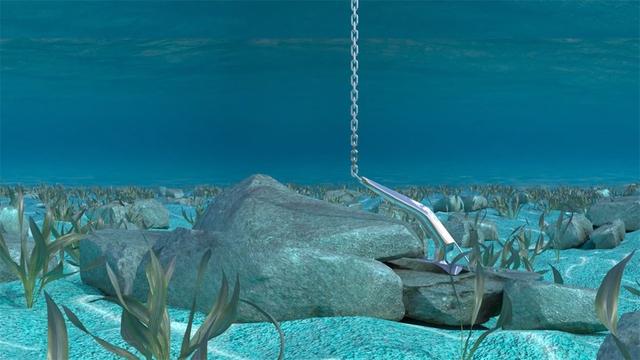
2. Proper Anchor Deployment Techniques
(1) Correct Anchor Angle and Scope
Achieving the right anchor angle and scope during deployment is essential for maximizing holding power. An anchor should ideally set at a horizontal angle to the seabed, allowing its flukes to dig in effectively. Proper scope, the ratio of anchor rode length to water depth, ensures that the anchor remains securely embedded. Understanding and adhering to recommended scope ratios based on the anchor type contribute to reliable anchoring performance.
(2) Best Practices for Setting the Anchor in Different Seabeds
Different seabed compositions demand varying techniques for setting the anchor securely. Soft, silty bottoms may require a slow and controlled drop to allow the anchor to bury itself, while hard or rocky bottoms may benefit from a more forceful drop to encourage penetration. Familiarizing oneself with the specific characteristics of the seabed and adjusting deployment techniques accordingly is key to successful anchoring.
3. Monitoring Anchor Drag and Adjusting as Needed
(1) Using Anchor Alarms and Sensors
Modern technology offers valuable tools for monitoring anchor performance, and the use of anchor alarms and sensors is highly recommended. Anchor alarms can alert users to any movement or dragging, prompting timely adjustments. Sensors that measure anchor load and tension provide real-time data on the anchor’s status, allowing for proactive responses to changing conditions.
(2) Regularly Checking Anchor Position During Anchoring
Even with advanced monitoring systems, it is essential to visually inspect the anchor’s position during anchoring. Changes in wind or current conditions can impact the vessel’s orientation, and periodic checks ensure that the anchor remains set and securely holding the vessel in place. This hands-on approach complements technological aids and adds an extra layer of assurance to the anchoring process.
Maintenance Guidelines for HHP Anchors
Anchors are vital components of a vessel’s equipment, and their reliability hinges on regular maintenance to ensure optimal performance. High Holding Power (HHP) anchors, designed for robust holding capacity, are no exception. To prolong their lifespan and maintain their effectiveness, it is imperative to follow comprehensive maintenance guidelines. In this section, we will explore key practices for the regular inspection, cleaning, and timely replacement of anchor components, highlighting the importance of proactive maintenance in preserving the integrity of HHP anchors.
1 Regular Inspection of the Anchor and Its Components
(1) Checking for Signs of Corrosion and Wear
Corrosion and wear are natural adversaries of marine equipment, and HHP anchors are no exception. Regular visual inspections are crucial to identify any signs of corrosion on the anchor body, flukes, or shank. Additionally, inspecting for wear on contact points and load-bearing areas ensures that the anchor maintains its structural integrity. Early detection of corrosion or wear allows for prompt intervention, preventing potential anchor failures.
(2) Inspecting the Anchor Chain and Shackles
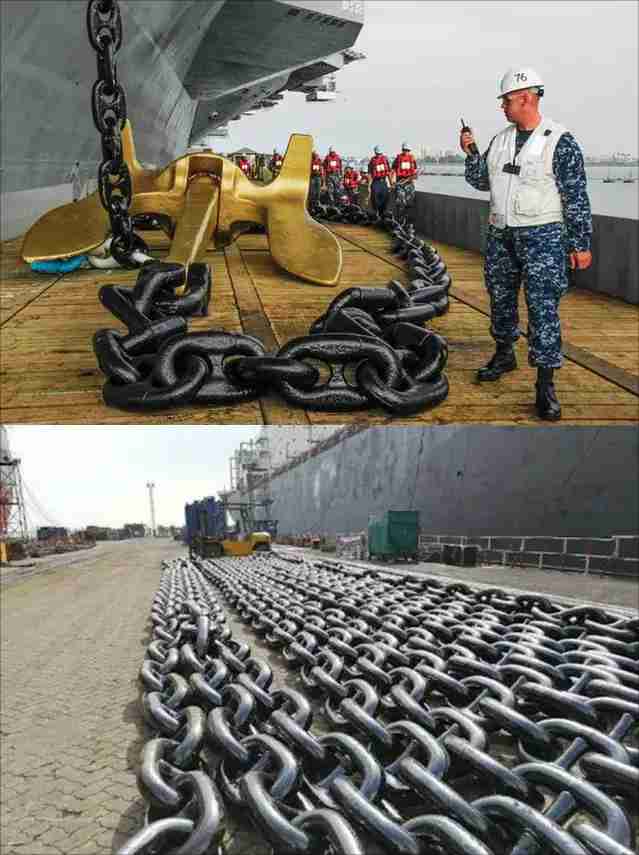
The anchor chain and shackles are integral components of the anchoring system, playing a pivotal role in transmitting the load from the anchor to the vessel. Regular inspections of the anchor chain for signs of corrosion, deformation, or weakened links are essential. Similarly, examining shackles for proper pin alignment and overall condition ensures the entire anchoring system functions seamlessly. Addressing issues with the chain and shackles proactively contributes to the overall safety and reliability of the anchoring setup.
2. Cleaning and Maintaining the Anchor
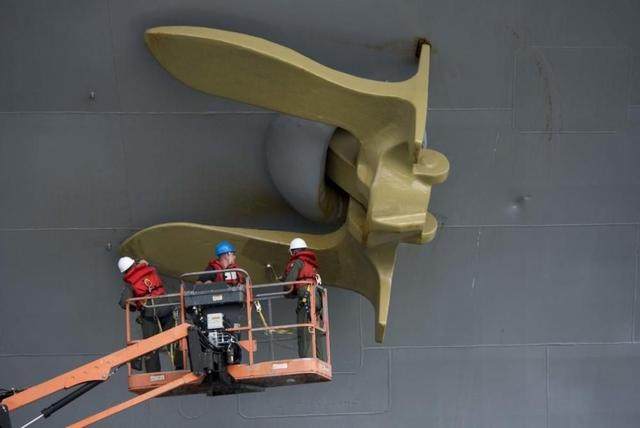
(1) Removing Mud, Sand, and Debris
Anchors are exposed to various seabed conditions, and the accumulation of mud, sand, and debris can impede their performance. After each use, it is advisable to clean the anchor thoroughly to remove any foreign materials. Paying special attention to the flukes and hinges ensures that the anchor can be set properly during future deployments. Regular cleaning not only maintains the anchor’s efficiency but also prevents unnecessary wear and tear.
(2) Lubricating Moving Parts for Smooth Operation
Many HHP anchors feature moving parts, such as hinges or swivels, that benefit from proper lubrication. Applying marine-grade lubricants to these moving components reduces friction, ensures smooth operation during deployment and retrieval, and helps prevent corrosion. Regular lubrication is a simple yet effective measure to enhance the overall functionality and longevity of the anchor.
3. Replacing Worn or Damaged Parts Promptly
(1) Identifying Common Issues and Their Solutions
Regular maintenance includes a proactive approach to identifying common issues associated with HHP anchors. This may involve inspecting for stress fractures, bent flukes, or misalignments in moving parts. Understanding these common issues allows users to implement timely solutions and prevent further damage to the anchor.
(2) Importance of Using High-Quality Replacement Parts
When replacement becomes necessary, it is paramount to use high-quality, manufacturer-approved parts. Substituting components with inferior alternatives can compromise the anchor’s performance and safety. Adhering to recommended replacement parts and procedures ensures that the anchor maintains its original design specifications and continues to deliver reliable performance.
Conclusion
As vessels navigate diverse waters and face varying seabed conditions, the selection, deployment, and maintenance of anchors become critical factors in the overall safety and efficiency of the anchoring process. Proper use involves a careful consideration of the vessel’s size, the characteristics of the seabed, and the adoption of correct deployment techniques. Meanwhile, meticulous maintenance practices, as outlined in the preceding sections, ensure that HHP anchors continue to function at their peak, resisting corrosion, wear, and the accumulation of debris.
As the maritime community strives for excellence in vessel operations, the commitment to proper anchor use and maintenance serves as a cornerstone in fostering a safer, more reliable, and environmentally conscious maritime environment. By following these guidelines, mariners can navigate with confidence, knowing that their anchors are not just equipment but dependable guardians ensuring the security of their vessels on the high seas.